锅炉水处理智能加药综合控制系统
一、 系统概述
a) 锅炉加药的意义
火力发电厂热力系统中水汽的品质的好坏,是影响火力发电厂热力设备(锅炉、汽轮机等)安全、经济运行的重要因素之一。为了防止热力设备的结垢、积盐和腐蚀,提高水汽品质,确保热力设备安全、高效运行,延长设备寿命,必须在锅炉给水和炉水中加入所需药品,进行化学水处理。
在锅炉给水中加入一定的氨和联氨,以及在炉水中加入一定的磷酸盐是锅炉化学水处理的常用方法,氨主要用来提高给水的PH值,防止游离二氧化碳对给水系统造成的酸性腐蚀,联氨主要用来除去给水中的残留氧,防止残留氧造成的氧腐蚀。在锅炉炉水加入磷酸盐的作用是除去炉水中的钙、镁离子,防止结垢,避免酸性和碱性腐蚀。
b) 现状
目前国内部分火电厂加药装置仍采用人工定时取样分析,手动调节柱塞式计量泵行程的方法对锅炉加药装置进行控制,这样不利于水汽品质质量的连续准确控制,不利于热力设备的安全运行。采用人工取样调节存在很多人为的因素,如人的个体差异、化验分析误差、责任心等,而其产生的影响和造成的后果在短时间内难以发觉,但设备的不良影响却是长久的、严重的。随着计算机技术、自动控制技术高速发展,PLC、变频器、在线仪表等的广泛应用,电厂加药自动化技术也已基本发展成了成熟的技术。目前国外的火电厂化水加氨、联氨、磷酸盐装置大多采用自动化控制装置,甚至已经达到无人值守的水平。我国近年来新建电厂的加药装置大都已经进行了自动化控制,加药系统自动化控制已是一种必然的趋势。
c) 新的解决方案
近年来,人们开始采用变频调速进行自动加药,由于不需要对管路进行改造,系统可靠,取得了良好的效果,这些控制系统大多采用常规PID算法。随着高参数、大容量机组的迅速发展及电厂管理水平的不断提高,人们对发电机组水汽指标的分析及加药系统的自动控制水平提出了更高的要求。四川诚讯科技公司根据客户需求,及时开发出BMCS-3型锅炉水处理智能加药综合控制系统,针对锅炉化学水处理具有大滞后、时变、非线性的特点,采用智能鲁棒控制算法(Intelligent Robust Control Algorithm),使锅炉加药控制水平上了一个新台阶,它既有较好的快速性,又有迟滞(死区)控制的稳定性和抗干扰能力,成功应用于各火电厂。
二、 系统组成原理
BMCS-3型锅炉水处理智能加药综合控制系统由水质仪表自动检测部分、加药装置、PLC控制系统和上位机系统四部分组成。
系统原理图如下:
1、水质仪表自动检测部分
水质仪表自动检测部分由取样装置和各种在线分析仪表组成。
取样装置完成对样水的减温、减压等预处理及人工取样,为在线仪表提供合格的样水。
在线分析仪表由PH表、电导表、联氨表、氧表、磷酸根表等组成,安装在仪表屏上。
PH表、电导表实时采集给水的PH值、电导值,经过变送器将信号送到PLC控制系统A/D转换模块,经CPU对输入数据进行分析计算后,将结果送上位机实时监测,为给水自动加氨提供控制信号。
联氨表、氧表实时采集给水的联氨余量、含氧值,经过变送器将信号送到PLC控制系统A/D转换模块,经CPU对输入数据进行分析计算后,将结果送上位机实时监测,为给水自动加联氨提供控制信号。
磷酸根表、PH表实时采集炉水的磷酸根值、PH值,经过变送器将信号送到PLC控制系统A/D转换模块,经CPU对输入数据进行分析计算后,将结果送上位机实时监测,为炉水自动加磷酸盐提供控制信号。
2、加药装置
加药装置由底座、加药箱、搅拌器、液位计、加药泵、变频器、电气控制柜、压力表、安全阀、稳压器以及加药管道、阀门等组成。加药装置在与PLC控制系统断开的情况下,可在电气控制柜上操作完成手动加药。
火电厂典型的自动加药系统共有三个:给水自动加氨系统、给水自动加联氨系统和炉水自动加磷酸盐系统,这三个自动加药系统从构成上基本一样,只是加药的工艺原理和参数设置上有所区别。
2.1给水自动加氨
PH表、电导表实时采集给水的PH值、电导值,经过变送器将信号送到A/D转换模块,由CPU对输入数据进行分析计算、制定控制方案由D/A转换模块变送后控制变频器输出,最后由变频器控制加氨泵完成给水自动加氨。电导表和PH表互为备用。当电导表和PH表均运行正常时,电导表作为导前微分信号,加快调节过程,PH表作为最终调节量,使系统以较快的速度进入稳定状态。
自动加氨控制系统如图1所示。系统由取样管路、PH表、电导表、控制器、变频器、加药泵、加药管路等组成。
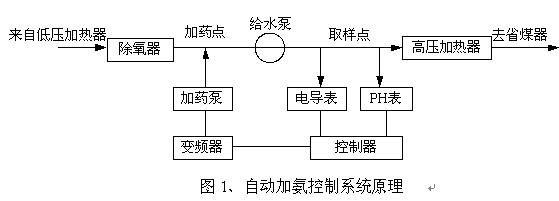
图1、自动加氨控制系统原理
控制器是整个系统的核心,它根据pH表和电导表的指示值通过运算确定变频器的频率,进而控制加药泵电机的转速,达到控制加药量的目的。图1所示的自动加氨控制系统可以等效为如下的方框图。

图2、自动加氨控制系统等效框图
2.2 给水自动加联氨
联氨表、氧表实时采集给水的联氨余量、含氧量,经过变送器将信号送到A/D转换装置,由CPU对输入数据进行分析计算、制定控制方案由D/A转换模块变送后控制变频器输出,最后由变频器控制加联氨泵完面给水自动加联氨。
给水自动加联氨系统如图3所示。系统由取样管路、联氨表、控制器、变频器、加药泵、加药管路等成。

图3、给水自动加联氨系统原理
控制器是整个系统的核心,它根据联氨表的指示值通过运算确定变频器的频率,进而控制电机的转速,达到控制加药量的目的。图3示的给水自动加联氨可以等效为如下的方框图:
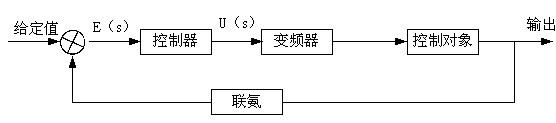
图4、给水自动加联氨系统等效框图
2.3 炉水自动加磷酸盐
系统自动采集炉水磷酸根表、PH表传来的信号,由CPU对输入数据进行分析计算,计算出R值,以R值确定二钠和三钠的配比,以磷酸根的含量作为加药的依据,系统自动制定控制方案由D/A转换模块变送后控制变频器的输出,最后由变频器控制加药泵完成自动加磷酸盐的过程。
磷酸盐协调处理控制系统由取样管路、pH表、磷酸根表、控制器、加药泵、加药管路等组成,如图5所示。
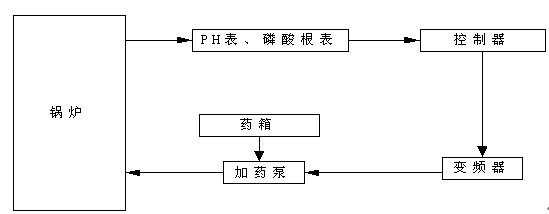
图5、协调磷酸盐处理自动控制系统原理图
控制器根据PH值、磷酸根值,经过计算R值,对系统进行控制。控制系统的等效框图如图6所示。

图6、 自动加磷酸盐系统等效框图
3、PLC控制系统
PLC控制系统是系统的核心,采用西门子、欧姆龙等通用流行的控制器,集成智能鲁棒控制算法,对加药实施控制,真正意义上实现自动加药。
PLC控制系统主要由电源模块、CPU模块、A/D模块、D/A模块、DI、DO模块以及通讯模块组成,根据现场需要可配置触摸屏进行本地显示和操作。
4、上位机系统
上位机系统由工控机、液晶显示器组成,通过通讯模块与PLC控制系统实现通讯和数据传送。采用图形组态软件(如WINCC等)组态实现汽水品质在线监测和自动加药的各种监控。实现监测数据集中实时显示、自动存档、越限自动报警、自动生成统计和管理报表等功能。
三、 系统功能
主要功能:
1、实时显示功能
可实现汽水品质指标的给水PH值、电导率、联氨值、溶解氧、炉水磷酸根、炉水PH值的实时显示,并可进行实时曲线显示,同时可实现加药现场的药液箱液位、加药泵运行状态等进行实时显示。
2、越限报警功能
对超标的水质指标、药液箱液位和各种故障进行报警。
3、参数设定功能
可在线设定仪表的量程、水质指标报警上下限、自动加药的给定值、采样时间等各种参数。
4、报表管理功能
根据用户需要,可生成各种应用报表,便于存档管理。
5、数据追忆功能
对历史数据和故障记录可进行查询和追忆。
6、自动控制功能
通过智能鲁棒控制算法,根据现场工况,自动控制加药量,将锅炉给水、炉水水质指标控制在规定范围,实现锅炉汽水的品质控制。
7、打印功能
可后台打印各种报表和数据。
8、联网通信功能
可将系统引入远端客户机、实现数据的远程监控。
四、 系统特点
1、控制方式灵活多变:既可以本地控制、也可以远程控制;既可以手动控制、也可以自动控制。自动控制时,PLC接收样水仪表的信号,根据样水表示值的变化规律,来自动调节控制输出量,由变频器输出0~50Hz控制量自动调节加药泵电机的转速,实现自动控制加药量。手动控制时,可将变频器置于工频,人工调节计量泵行程来实现加药量的增减变化;也可固定计量泵行程,人工手动调节变频器频率(远程调节可在上位机上输入加药泵变频器频率,本地可通过控制柜调频旋钮实现加药泵变频器频率的调节)。
2、显示直观、操作简单:就地显示溶液箱液位及变频器频率,可现场通过调频旋(按)钮进行调频,操作简单,上位机能直观的显示液位值、给水PH值、电导率、联氨值、溶解氧、炉水磷酸根、炉水PH值,可在界面上拖动滑块手动改变变频器频率值,汉字操作界面,使用简单方便,即使非专业人员,只要稍加培训即可操作。
3、智能、自动化程度高:系统针对大延时控制系统,运用“鲁棒技术”、变结构技术和仿人工智能控制思想,采用智能鲁棒控制算法,使得控制器模拟人的控制行为,同时发挥计算机的在线优势,实现系统快速稳定调节,可靠性高,加药精度高,能够有效满足电厂的运行要求,自动化程度高。
五、 技术指标
1、数据采样频次:连续
2、技术指标控制范围
给水加氨
给水PH值 8.8~9.3 (可调节范围)
电导值(H+交换柱) ≤0.3μs/cm(可调节范围)
给水加联胺
联氨余量 10~50μg/L(可调节范围)
溶解氧 正常状态≤7μg/L(可调节范围)
炉水加磷酸盐
炉水PH值 9~10 (可调节范围)
炉水磷酸根 2~10 (可调节范围)
R值 2.3~2.8 (可调节范围)
3、使用环境温度:-20~50℃
使用环境湿度:5~95%
电源要求:~220V 50Hz
4、控制方式:手动或自动;本地或远程。
六、 智能鲁棒控制算法
自动控制系统等效框图如下:
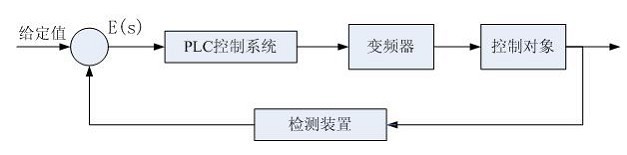
因为电厂的整个加药系统和取样系统的管路很长,机组的负荷又处在一个动态的变化中,变化范围大,对控制造成相对的难度。各电厂根据自己的加药系统特性,采用的控制算法是不一样的,较普遍采用的PID算法和逐次逼近法,都是通过推导公式算出一个控制周期内的加药量进行控制。由于本系统的控制对象为大延时滞后对象(τ/T>10~100),采用普通PID算法难以达到稳定的控制,因此系统采用“鲁棒技术”、变结构控制技术和仿人工智能控制思想,采用智能鲁棒控制算法,使得控制器模拟人的控制行为,同时发挥计算机的在线控制优势,实现系统快速稳定调节。基础的控制算法采用PI。
其中比例系数 和积分系数 是误差的函数,误差e在不同的状态下, 和 的取值将有所不同,这样将有利于系统的稳定和稳态误差的减小。
系统的广义控制对象由变频器、锅炉、取样系统、仪表等组成。它的等效数学模型可以用一阶惯性环节加纯延迟来表示:
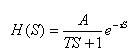
由于对象特性的差异,特别是纯延迟时间的不同,我们可以选择不同的控制算法。常用的算法是PID规律。因为锅炉加药是一个缓慢变化的过程,所以在锅炉加药控制中主要使用PI算法。下面我们来讨论基于PI的几种算法。
1、常规PI控制算法
在锅炉加药控制系统中我们常采用位置式PI算法,其数学表达式为
这是一种应用非常广泛的控制规律,它适用于 的控制对象。对于锅炉加药系统来说,这种算法适用于取样管较短,即延迟时间较小的场合。
2、智能鲁棒控制算法
由于常规PI算法在锅炉加药系统中的应用受到了限制,我们可以采用下面几种改进PI算法组合为智能鲁棒控制算法。
积分分离PI控制算法
系统中加入积分校正以后,会产生过大的超调量。为了减小超调,我们可以引进积分分离算法,使得控制系统的性能得到较大的改善。积分分离算法要设置分离阈 。
(a) 当
时,即偏差值较小时,采用常规PI算法,可保证系统的控制精度。
(b) 当
时,即偏差值较大时,采用常规P算法,可保证系统的超调量大幅度降低。
积分分离PI算法可表示为
式中
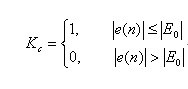
抗控制作用饱和的PI算法
由于长期存在偏差或偏差较大,计算出的控制量有可能出现饱和而溢出。如果执行机构已到极限位置仍然不能消除偏差时,由于积分作用,控制量继续增大或减小,而执行机构已无相应的动作。当出现积分饱和时,势必使超调量增加,控制品质变坏。作为防止积分饱和的办法之一,可对运算出的控制量u(n)限幅,同时停止积分作用。其算法可以用下式来描述:
式中
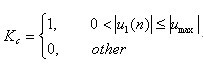
组合算法
由上述算法组成的智能鲁棒控制算法可用下式描述:
式中
这种算法具有较强的鲁棒性。
七、 工程案例
1、攀钢发电厂1#、2#、3#机组锅炉;
2、攀钢能动中心一期4台25MW机组锅炉。
锅炉水处理智能加药综合控制系统
一、 系统概述
a) 锅炉加药的意义
火力发电厂热力系统中水汽的品质的好坏,是影响火力发电厂热力设备(锅炉、汽轮机等)安全、经济运行的重要因素之一。为了防止热力设备的结垢、积盐和腐蚀,提高水汽品质,确保热力设备安全、高效运行,延长设备寿命,必须在锅炉给水和炉水中加入所需药品,进行化学水处理。
在锅炉给水中加入一定的氨和联氨,以及在炉水中加入一定的磷酸盐是锅炉化学水处理的常用方法,氨主要用来提高给水的PH值,防止游离二氧化碳对给水系统造成的酸性腐蚀,联氨主要用来除去给水中的残留氧,防止残留氧造成的氧腐蚀。在锅炉炉水加入磷酸盐的作用是除去炉水中的钙、镁离子,防止结垢,避免酸性和碱性腐蚀。
b) 现状
目前国内部分火电厂加药装置仍采用人工定时取样分析,手动调节柱塞式计量泵行程的方法对锅炉加药装置进行控制,这样不利于水汽品质质量的连续准确控制,不利于热力设备的安全运行。采用人工取样调节存在很多人为的因素,如人的个体差异、化验分析误差、责任心等,而其产生的影响和造成的后果在短时间内难以发觉,但设备的不良影响却是长久的、严重的。随着计算机技术、自动控制技术高速发展,PLC、变频器、在线仪表等的广泛应用,电厂加药自动化技术也已基本发展成了成熟的技术。目前国外的火电厂化水加氨、联氨、磷酸盐装置大多采用自动化控制装置,甚至已经达到无人值守的水平。我国近年来新建电厂的加药装置大都已经进行了自动化控制,加药系统自动化控制已是一种必然的趋势。
c) 新的解决方案
近年来,人们开始采用变频调速进行自动加药,由于不需要对管路进行改造,系统可靠,取得了良好的效果,这些控制系统大多采用常规PID算法。随着高参数、大容量机组的迅速发展及电厂管理水平的不断提高,人们对发电机组水汽指标的分析及加药系统的自动控制水平提出了更高的要求。四川诚讯科技公司根据客户需求,及时开发出BMCS-3型锅炉水处理智能加药综合控制系统,针对锅炉化学水处理具有大滞后、时变、非线性的特点,采用智能鲁棒控制算法(Intelligent Robust Control Algorithm),使锅炉加药控制水平上了一个新台阶,它既有较好的快速性,又有迟滞(死区)控制的稳定性和抗干扰能力,成功应用于各火电厂。
二、 系统组成原理
BMCS-3型锅炉水处理智能加药综合控制系统由水质仪表自动检测部分、加药装置、PLC控制系统和上位机系统四部分组成。
系统原理图如下:
1、水质仪表自动检测部分
水质仪表自动检测部分由取样装置和各种在线分析仪表组成。
取样装置完成对样水的减温、减压等预处理及人工取样,为在线仪表提供合格的样水。
在线分析仪表由PH表、电导表、联氨表、氧表、磷酸根表等组成,安装在仪表屏上。
PH表、电导表实时采集给水的PH值、电导值,经过变送器将信号送到PLC控制系统A/D转换模块,经CPU对输入数据进行分析计算后,将结果送上位机实时监测,为给水自动加氨提供控制信号。
联氨表、氧表实时采集给水的联氨余量、含氧值,经过变送器将信号送到PLC控制系统A/D转换模块,经CPU对输入数据进行分析计算后,将结果送上位机实时监测,为给水自动加联氨提供控制信号。
磷酸根表、PH表实时采集炉水的磷酸根值、PH值,经过变送器将信号送到PLC控制系统A/D转换模块,经CPU对输入数据进行分析计算后,将结果送上位机实时监测,为炉水自动加磷酸盐提供控制信号。
2、加药装置
加药装置由底座、加药箱、搅拌器、液位计、加药泵、变频器、电气控制柜、压力表、安全阀、稳压器以及加药管道、阀门等组成。加药装置在与PLC控制系统断开的情况下,可在电气控制柜上操作完成手动加药。
火电厂典型的自动加药系统共有三个:给水自动加氨系统、给水自动加联氨系统和炉水自动加磷酸盐系统,这三个自动加药系统从构成上基本一样,只是加药的工艺原理和参数设置上有所区别。
2.1给水自动加氨
PH表、电导表实时采集给水的PH值、电导值,经过变送器将信号送到A/D转换模块,由CPU对输入数据进行分析计算、制定控制方案由D/A转换模块变送后控制变频器输出,最后由变频器控制加氨泵完成给水自动加氨。电导表和PH表互为备用。当电导表和PH表均运行正常时,电导表作为导前微分信号,加快调节过程,PH表作为最终调节量,使系统以较快的速度进入稳定状态。
自动加氨控制系统如图1所示。系统由取样管路、PH表、电导表、控制器、变频器、加药泵、加药管路等组成。
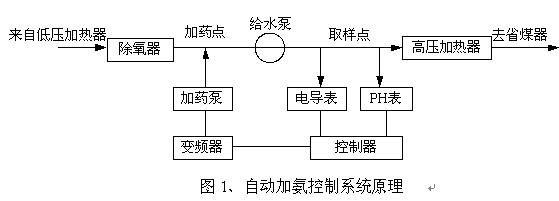
图1、自动加氨控制系统原理
控制器是整个系统的核心,它根据pH表和电导表的指示值通过运算确定变频器的频率,进而控制加药泵电机的转速,达到控制加药量的目的。图1所示的自动加氨控制系统可以等效为如下的方框图。

图2、自动加氨控制系统等效框图
2.2 给水自动加联氨
联氨表、氧表实时采集给水的联氨余量、含氧量,经过变送器将信号送到A/D转换装置,由CPU对输入数据进行分析计算、制定控制方案由D/A转换模块变送后控制变频器输出,最后由变频器控制加联氨泵完面给水自动加联氨。
给水自动加联氨系统如图3所示。系统由取样管路、联氨表、控制器、变频器、加药泵、加药管路等成。

图3、给水自动加联氨系统原理
控制器是整个系统的核心,它根据联氨表的指示值通过运算确定变频器的频率,进而控制电机的转速,达到控制加药量的目的。图3示的给水自动加联氨可以等效为如下的方框图:
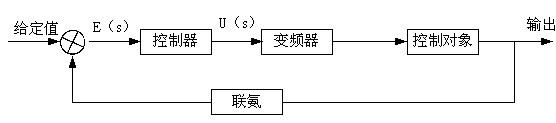
图4、给水自动加联氨系统等效框图
2.3 炉水自动加磷酸盐
系统自动采集炉水磷酸根表、PH表传来的信号,由CPU对输入数据进行分析计算,计算出R值,以R值确定二钠和三钠的配比,以磷酸根的含量作为加药的依据,系统自动制定控制方案由D/A转换模块变送后控制变频器的输出,最后由变频器控制加药泵完成自动加磷酸盐的过程。
磷酸盐协调处理控制系统由取样管路、pH表、磷酸根表、控制器、加药泵、加药管路等组成,如图5所示。
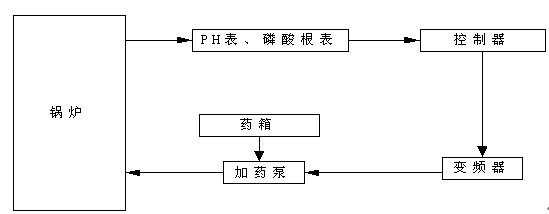
图5、协调磷酸盐处理自动控制系统原理图
控制器根据PH值、磷酸根值,经过计算R值,对系统进行控制。控制系统的等效框图如图6所示。

图6、 自动加磷酸盐系统等效框图
3、PLC控制系统
PLC控制系统是系统的核心,采用西门子、欧姆龙等通用流行的控制器,集成智能鲁棒控制算法,对加药实施控制,真正意义上实现自动加药。
PLC控制系统主要由电源模块、CPU模块、A/D模块、D/A模块、DI、DO模块以及通讯模块组成,根据现场需要可配置触摸屏进行本地显示和操作。
4、上位机系统
上位机系统由工控机、液晶显示器组成,通过通讯模块与PLC控制系统实现通讯和数据传送。采用图形组态软件(如WINCC等)组态实现汽水品质在线监测和自动加药的各种监控。实现监测数据集中实时显示、自动存档、越限自动报警、自动生成统计和管理报表等功能。
三、 系统功能
主要功能:
1、实时显示功能
可实现汽水品质指标的给水PH值、电导率、联氨值、溶解氧、炉水磷酸根、炉水PH值的实时显示,并可进行实时曲线显示,同时可实现加药现场的药液箱液位、加药泵运行状态等进行实时显示。
2、越限报警功能
对超标的水质指标、药液箱液位和各种故障进行报警。
3、参数设定功能
可在线设定仪表的量程、水质指标报警上下限、自动加药的给定值、采样时间等各种参数。
4、报表管理功能
根据用户需要,可生成各种应用报表,便于存档管理。
5、数据追忆功能
对历史数据和故障记录可进行查询和追忆。
6、自动控制功能
通过智能鲁棒控制算法,根据现场工况,自动控制加药量,将锅炉给水、炉水水质指标控制在规定范围,实现锅炉汽水的品质控制。
7、打印功能
可后台打印各种报表和数据。
8、联网通信功能
可将系统引入远端客户机、实现数据的远程监控。
四、 系统特点
1、控制方式灵活多变:既可以本地控制、也可以远程控制;既可以手动控制、也可以自动控制。自动控制时,PLC接收样水仪表的信号,根据样水表示值的变化规律,来自动调节控制输出量,由变频器输出0~50Hz控制量自动调节加药泵电机的转速,实现自动控制加药量。手动控制时,可将变频器置于工频,人工调节计量泵行程来实现加药量的增减变化;也可固定计量泵行程,人工手动调节变频器频率(远程调节可在上位机上输入加药泵变频器频率,本地可通过控制柜调频旋钮实现加药泵变频器频率的调节)。
2、显示直观、操作简单:就地显示溶液箱液位及变频器频率,可现场通过调频旋(按)钮进行调频,操作简单,上位机能直观的显示液位值、给水PH值、电导率、联氨值、溶解氧、炉水磷酸根、炉水PH值,可在界面上拖动滑块手动改变变频器频率值,汉字操作界面,使用简单方便,即使非专业人员,只要稍加培训即可操作。
3、智能、自动化程度高:系统针对大延时控制系统,运用“鲁棒技术”、变结构技术和仿人工智能控制思想,采用智能鲁棒控制算法,使得控制器模拟人的控制行为,同时发挥计算机的在线优势,实现系统快速稳定调节,可靠性高,加药精度高,能够有效满足电厂的运行要求,自动化程度高。
五、 技术指标
1、数据采样频次:连续
2、技术指标控制范围
给水加氨
给水PH值 8.8~9.3 (可调节范围)
电导值(H+交换柱) ≤0.3μs/cm(可调节范围)
给水加联胺
联氨余量 10~50μg/L(可调节范围)
溶解氧 正常状态≤7μg/L(可调节范围)
炉水加磷酸盐
炉水PH值 9~10 (可调节范围)
炉水磷酸根 2~10 (可调节范围)
R值 2.3~2.8 (可调节范围)
3、使用环境温度:-20~50℃
使用环境湿度:5~95%
电源要求:~220V 50Hz
4、控制方式:手动或自动;本地或远程。
六、 智能鲁棒控制算法
自动控制系统等效框图如下:
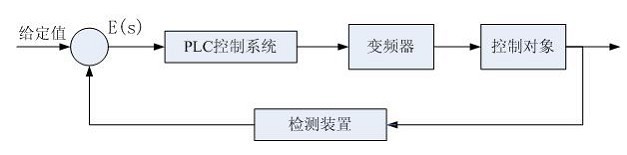
因为电厂的整个加药系统和取样系统的管路很长,机组的负荷又处在一个动态的变化中,变化范围大,对控制造成相对的难度。各电厂根据自己的加药系统特性,采用的控制算法是不一样的,较普遍采用的PID算法和逐次逼近法,都是通过推导公式算出一个控制周期内的加药量进行控制。由于本系统的控制对象为大延时滞后对象(τ/T>10~100),采用普通PID算法难以达到稳定的控制,因此系统采用“鲁棒技术”、变结构控制技术和仿人工智能控制思想,采用智能鲁棒控制算法,使得控制器模拟人的控制行为,同时发挥计算机的在线控制优势,实现系统快速稳定调节。基础的控制算法采用PI。
其中比例系数 和积分系数 是误差的函数,误差e在不同的状态下, 和 的取值将有所不同,这样将有利于系统的稳定和稳态误差的减小。
系统的广义控制对象由变频器、锅炉、取样系统、仪表等组成。它的等效数学模型可以用一阶惯性环节加纯延迟来表示:
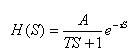
由于对象特性的差异,特别是纯延迟时间的不同,我们可以选择不同的控制算法。常用的算法是PID规律。因为锅炉加药是一个缓慢变化的过程,所以在锅炉加药控制中主要使用PI算法。下面我们来讨论基于PI的几种算法。
1、常规PI控制算法
在锅炉加药控制系统中我们常采用位置式PI算法,其数学表达式为
这是一种应用非常广泛的控制规律,它适用于 的控制对象。对于锅炉加药系统来说,这种算法适用于取样管较短,即延迟时间较小的场合。
2、智能鲁棒控制算法
由于常规PI算法在锅炉加药系统中的应用受到了限制,我们可以采用下面几种改进PI算法组合为智能鲁棒控制算法。
积分分离PI控制算法
系统中加入积分校正以后,会产生过大的超调量。为了减小超调,我们可以引进积分分离算法,使得控制系统的性能得到较大的改善。积分分离算法要设置分离阈 。
(a) 当
时,即偏差值较小时,采用常规PI算法,可保证系统的控制精度。
(b) 当
时,即偏差值较大时,采用常规P算法,可保证系统的超调量大幅度降低。
积分分离PI算法可表示为
式中
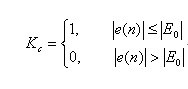
抗控制作用饱和的PI算法
由于长期存在偏差或偏差较大,计算出的控制量有可能出现饱和而溢出。如果执行机构已到极限位置仍然不能消除偏差时,由于积分作用,控制量继续增大或减小,而执行机构已无相应的动作。当出现积分饱和时,势必使超调量增加,控制品质变坏。作为防止积分饱和的办法之一,可对运算出的控制量u(n)限幅,同时停止积分作用。其算法可以用下式来描述:
式中
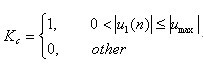
组合算法
由上述算法组成的智能鲁棒控制算法可用下式描述:
式中
这种算法具有较强的鲁棒性。
七、 工程案例
1、攀钢发电厂1#、2#、3#机组锅炉;
2、攀钢能动中心一期4台25MW机组锅炉。